What Are the Consequences for a Business in Kansas That Does Not Pass Its Eye-Wash Station Inspection?
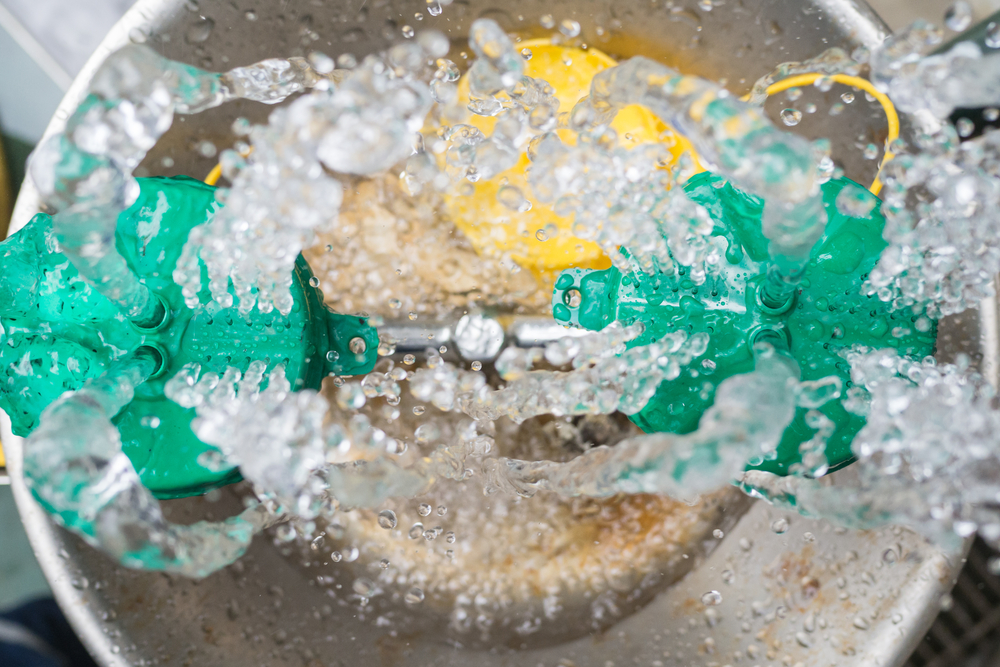
Businesses across Kansas, particularly those operating in industries where hazardous chemicals or materials are involved, must adhere to specific health and safety regulations. One of the critical safety measures for protecting employees in these environments is the installation of properly functioning eye-wash stations. These stations are required by law to provide immediate and effective eye irrigation in case of chemical exposure or other contaminants. However, when a business fails to pass its eye-wash station inspection, the consequences can be far-reaching, affecting not only employee safety but also the business’s compliance standing, financial health, and reputation.
The Importance of Eye-Wash Stations in Kansas Workplaces
Eye-wash stations are critical safety devices in workplaces that use chemicals, solvents, or other hazardous materials that could potentially cause serious eye injuries. These stations are designed to provide immediate relief by flushing harmful substances from the eyes, helping to prevent long-term damage and even permanent blindness. The Occupational Safety and Health Administration (OSHA) and the American National Standards Institute (ANSI) set strict guidelines for eye-wash stations in the workplace, outlining the required specifications and maintenance procedures.
In Kansas, businesses that use hazardous chemicals, especially those involved in manufacturing, laboratories, or cleaning industries, are mandated to provide these safety features as part of their workplace safety protocols. The state, in compliance with federal OSHA regulations, expects businesses to meet the necessary standards for eye-wash station functionality, positioning, and maintenance.
Legal and Regulatory Implications of Failing an Eye-Wash Station Inspection
When a business in Kansas fails to pass its eye-wash station inspection, the legal and regulatory consequences can be severe. The most immediate consequence is a citation from OSHA or local authorities for non-compliance with safety regulations. These citations can carry hefty fines and penalties, depending on the severity of the violation. The failure to meet OSHA’s standards for eye-wash stations could be considered a serious or even willful violation, leading to more significant financial penalties.
In addition to monetary fines, businesses that fail eye-wash station inspections may face increased scrutiny during subsequent inspections. Repeat violations or a pattern of non-compliance could lead to more substantial penalties and a higher likelihood of facing legal actions, including lawsuits from employees who may have been harmed due to the lack of proper safety equipment.
It’s essential for businesses to not only comply with these safety standards but to maintain a record of inspections, repairs, and any modifications made to the eye-wash stations. Failure to document these efforts could complicate matters during inspections and investigations, further increasing the risk of legal consequences.
Impact on Employee Health and Safety
The most pressing consequence of a failed eye-wash station inspection is the direct impact on employee health and safety. In the event of a chemical splash or irritant exposure to the eyes, the lack of a functional eye-wash station could lead to severe injury. Depending on the substance involved, prolonged exposure without proper eye irrigation can cause irreversible damage to the cornea, leading to permanent vision impairment or blindness.
Employees who suffer from injuries due to non-functional eye-wash stations may also experience long-term health issues that affect their quality of life. Additionally, the mental and emotional toll of a workplace injury can negatively impact an employee’s morale and productivity. If the injury is severe enough, it could result in prolonged absence from work, and in some cases, permanent disability.
Furthermore, in the event of an injury, the employer could face workers’ compensation claims. These claims can be costly, especially if the injury is a direct result of a failure to maintain proper safety equipment, such as eye-wash stations. Workers’ compensation claims, legal disputes, and the potential for employees to seek compensation through lawsuits can put significant financial strain on a business.
Financial Repercussions of Failing to Pass an Eye-Wash Station Inspection
In addition to the immediate fines and penalties imposed by regulatory bodies, the financial repercussions of a failed eye-wash station inspection can extend much further. The cost of maintaining an eye-wash station inspection schedule and repairing or upgrading faulty equipment can be considerable. However, when a business fails to meet compliance standards, it risks much higher financial consequences.
First, the cost of fines and penalties can be substantial. OSHA violations can range from a few hundred dollars for minor infractions to tens of thousands of dollars for more serious violations. For instance, a serious violation, such as failing to meet eye-wash station requirements, could lead to fines of up to $13,653 per violation. If the violation is deemed willful or repeated, the fine could increase to as much as $136,532. This level of financial penalty can significantly harm a business’s bottom line, particularly for smaller companies that may already be operating on tight margins.
Beyond direct fines, the cost of managing an injury or illness that could have been prevented with a functioning eye-wash station can add up quickly. Medical bills, workers’ compensation claims, and potential lawsuits can all contribute to substantial financial losses. The costs related to employee downtime, insurance premiums, and possible reputational damage can further impact a business’s financial stability.
Damage to Business Reputation and Consumer Trust
Beyond the legal and financial consequences, failing an eye-wash station inspection in Kansas can severely damage a business’s reputation. In today’s world, consumers and employees alike are increasingly conscious of workplace safety standards and corporate responsibility. A business that is cited for failing to meet safety regulations may find its reputation tarnished in the eyes of the public and its workforce.
For businesses that operate in industries with high exposure to hazardous materials, such as manufacturing, chemicals, or research, safety violations can be especially damaging. News of a failure to comply with safety regulations can spread quickly, especially in a tightly knit industry or community. Negative publicity can drive away potential customers and clients, while talented workers may look for safer environments to work in. In some cases, a poor safety record could make it difficult for businesses to attract new employees or maintain a loyal workforce.
When businesses fail to maintain eye-wash stations that meet regulatory standards, it can raise questions about their overall commitment to worker safety and well-being. This can have long-lasting effects on the trust customers place in the business, which can, in turn, lead to reduced sales, partnerships, and business opportunities.
Long-Term Consequences and Preventative Measures
The long-term consequences of failing an eye-wash station inspection in Kansas can be significant, but they are not inevitable. Businesses that take proactive steps to ensure that their eye-wash stations are properly installed, maintained, and inspected can avoid the majority of these risks. By regularly testing the equipment, keeping detailed records of maintenance, and ensuring that employees are trained in emergency procedures, businesses can maintain compliance and protect their workforce.
Regular eye-wash station inspections are not only a legal requirement but a moral obligation for businesses that operate in hazardous environments. By investing in safety measures and taking the time to ensure that all equipment is functioning correctly, businesses can avoid the potentially severe consequences of a failed inspection. This proactive approach can help safeguard employee health, maintain compliance with Kansas regulations, and protect the business’s reputation and financial health.
Conclusion
Failing to pass an eye-wash station inspection in Kansas can have serious consequences for businesses, including legal penalties, financial losses, and reputational damage. These outcomes underscore the importance of maintaining a safe working environment by ensuring that all safety equipment, including eye-wash stations, meets regulatory standards. Through diligent attention to safety and compliance, businesses can mitigate risks and ensure the well-being of their employees.
Need Life Safety Products In Garden City, KS?
There are various forms of personal protection. We offer fire safety and fire prevention equipment including fire extinguishers, and we service them, too. Business owners throughout Southwest Kansas should know what types of personal protection or fire safety equipment is necessary to suit the needs of their business. Rather than struggling with purchasing decisions, discuss with our consultants from C.F. Fire & Life Safety and let us guide you through the logistics. Based in Liberal, KS, C.F. Fire & Life Safety, is your destination for personal protection, fire safety, fire prevention, and fire extinguisher services throughout Southwest Kansas. Contact us today to learn more about what we can do for you!